Cryogenic Grinding Higher
2023-12-23T16:12:20+00:00
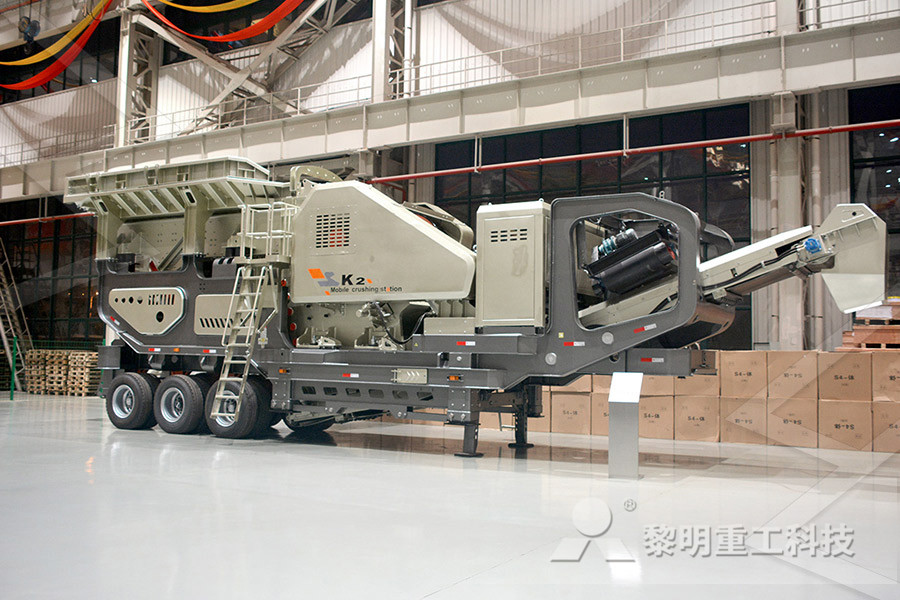
HIGHER THROUGHPUT FOR CRYOGENIC GRINDING
HIGHER THROUGHPUT FOR CRYOGENIC GRINDING Grinding and Pulverizing Tissue Homogenization and Cell Lysis The 6870D Freezer/Mill® is a highthroughput, dual chamber cryogenic grinder with a selfcontained liquid nitrogen tub and insulated case It chills samples in liquid nitrogen then pulverizes them with a magnetically driven impactor It Cryogenic grinding – which cools materials to embrittle them and improve their processabiilty – provides important advantages over grinding at ambient temperatures, particularly for materials that are too soft or too heat sensitive to be easily milled under routine conditions These advantages include: Increased production ratesCryogenic Grinding Presentation Union Process Cryogenic Grinding System When using the system, measurable and repeatable results are obtained for lab or productions calculations Mills range in size from 71/2 HP to 200 HP With our cryogenic grinding unit an understanding develops with interaction of equipment components and operating parameters Factors such as consistent feed rate, preciseMech Cryogenic Grinding Report
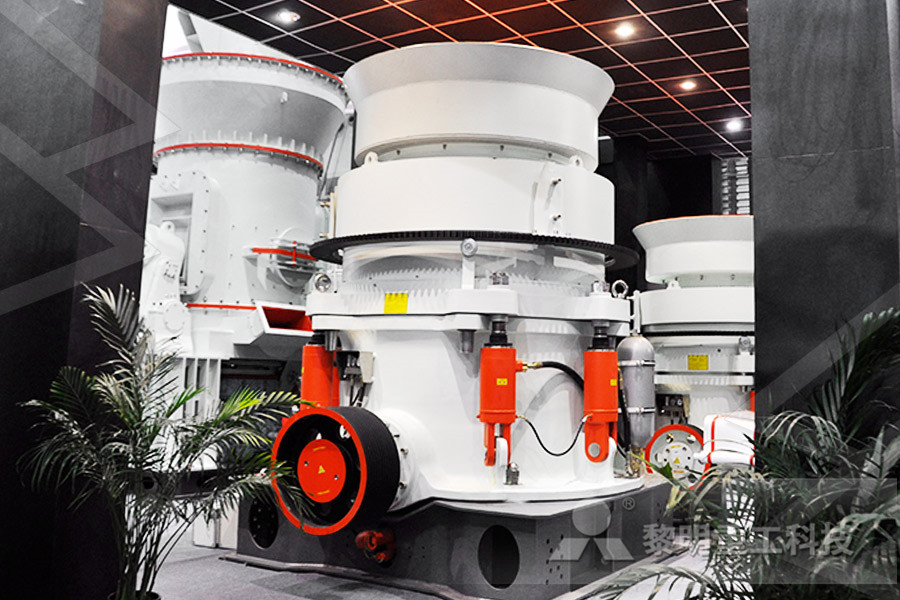
A Review on Cryogenic Grinding Inpressco
Cryogenic grinders have higher production rate along with it more uniform particle distribution The experimental data vary with different sized, nature of feed material and also with change in configuration setting of cryogenic grinding machine Table11Specifications for Cryogenic grinders Power consumption 160 watts A higher magnitude of compressive residual stresses was found to be induced under cryogenic grinding over the dry condition, which is also evident from Figure 7 In cryogenic grinding, the cooling occurs at a faster rate at the outer Effect of Cryogenic Grinding on Fatigue Life of Additively Cryogenic grinding with in a paddle screw cooler freezes the high fat or oil content in the regrind and makes it brittle The spices and foodstuffs remain freeflowing and are much easier to grind Cold grinding avoids the undesirable rise in temperature caused by the electrical energy of the mill motors and ensures high product qualityCold grinding cryogenic grinding with the aid of liquid
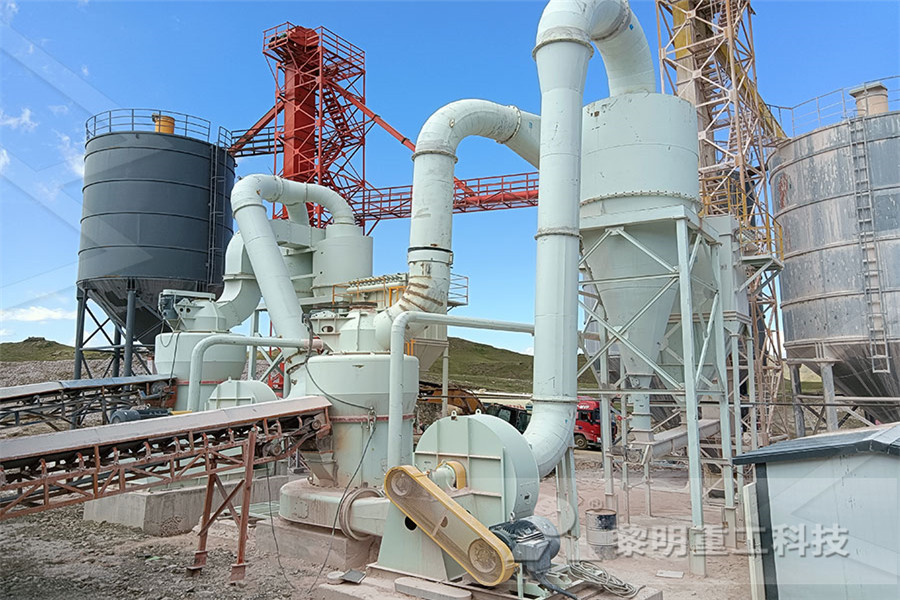
(PDF) A Review on Cryogenic Grinding ResearchGate
Similarly, cryogenic grinding is a term supported by the act of grinding a thing at very low temperature This technique is generally used to grind the material, which contains heat labile Cryogenic cooling (utilizing liquid Nitrogen or CO 2) can be a very effective method for the reduction of tool loading and improving the grinding process due to its high cooling rate Using cryogenic cooling, the cutting action is more than sliding and plowing Compared to liquid Nitrogen, CO 2 gas is more economical and also more userfriendlyThe effects of cryogenic cooling on the grinding process Cryogenic Grinding There are countless polymers that due to their low density and melting points, grinding with mills at a room temperature is not possible because the friction of the mill itself generates a temperature higher than the melting point of the polymer and therefore the polymer liquefy With cryogenic grinding we solve this problemGrinding Powder Plastic Europe
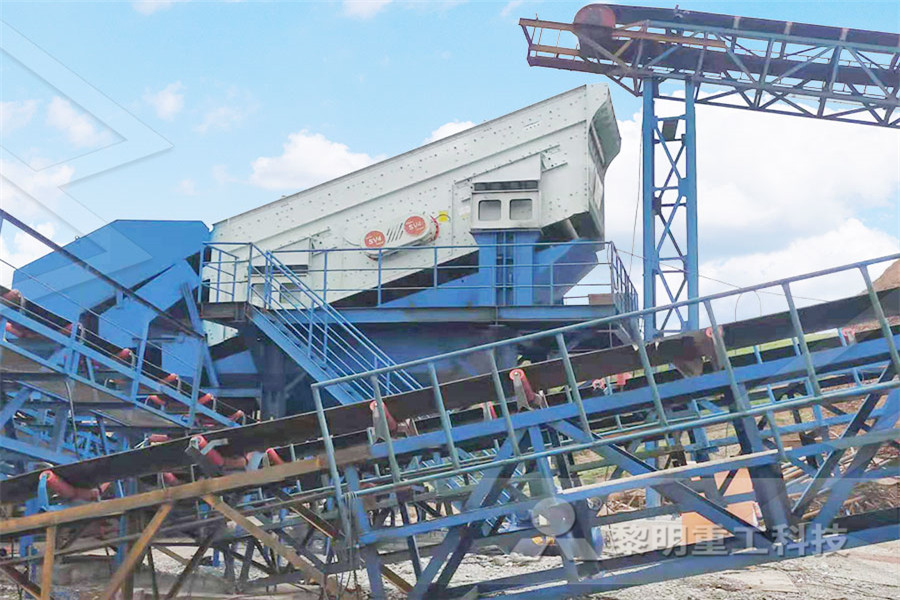
Key issues and challenges in spice grinding ScienceDirect
Cryogenic grinding ( Fig 1 ), a method in which liquid nitrogen (boiling point of −1956 °C) is being used to prefreeze the material before grinding ( Balasubramanian et al, 2012) and removing heat during grinding, is the advanced and effective method to maintain the quality of spices during grinding ( Saxena et al, 2015 ) HIGHER THROUGHPUT FOR CRYOGENIC GRINDING Grinding and Pulverizing Tissue Homogenization and Cell Lysis The 6870D Freezer/Mill® is a highthroughput, dual chamber cryogenic grinder with a selfcontained liquid nitrogen tub and insulated case It chills samples in liquid nitrogen then pulverizes them with a magnetically driven impactor It HIGHER THROUGHPUT FOR CRYOGENIC GRINDINGCryogenic grinding is most effective when the product is sprayed with liquid nitrogen as it is being conveyed and introduced into the Attritor An additional benefit of cryogenic milling in an internally agitated ball mill is the ability to fully immerse the product in liquid nitrogen during millingCryogenic Grinding Presentation Union Process
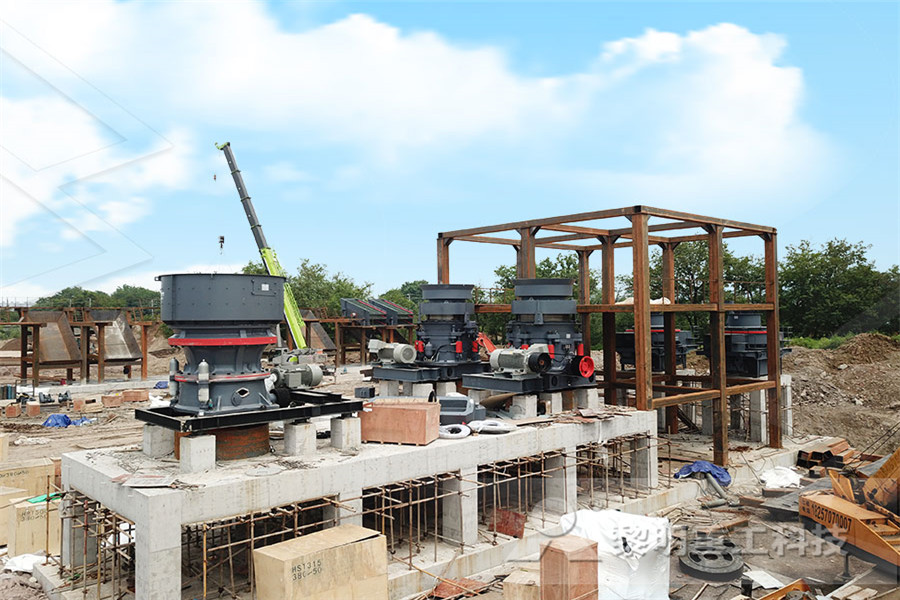
Mech Cryogenic Grinding Report
Cryogenic Grinding System When using the system, measurable and repeatable results are obtained for lab or productions calculations Mills range in size from 71/2 HP to 200 HP With our cryogenic grinding unit an understanding develops with interaction of equipment components and operating parameters Factors such as consistent feed rate, precise Cryogenic grinding provides higher production rate, lower energy consumption, finer particle size, more uniform particle distribution, lower grinding cost, no heat generation which is good while grinding spices and provides an inert atmosphere thus eliminating the CRYOGENIC GRINDING: A PHYSICAL TECHNIQUE TO ADVANTAGES OF CRYOGENIC GRINDING Higher material removal rate can be achieved Tool wear and tear is minimized to a great extent Grinding forces are reduced Cryogens act as coolant and hence the effects of overheating of the tool and work piece are reduced Materials which are soft and elastic in nature such as rubber can be easily machined CRYOGENIC GRINDING AND IT’S APPLICATIONS
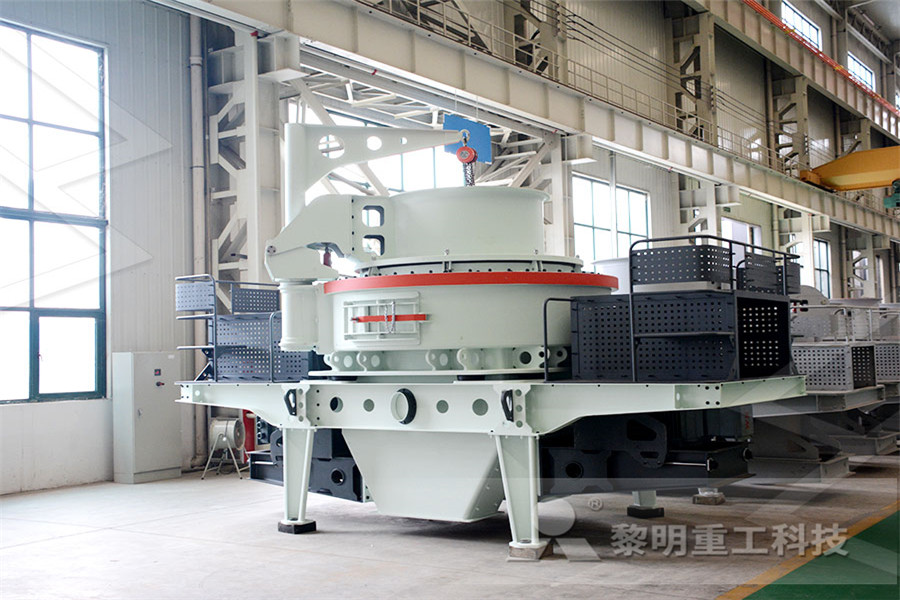
(PDF) A Review on Cryogenic Grinding
Similarly, cryogenic grinding is a term supported by the act of grinding a thing at very low temperature This technique is generally used to grind the material, which contains heat labile In 5 m/s cutting speed, the heat generation of grinding is less than 10 and 15 cutting speed Higher heat generation (at higher cutting speed) led to decrease grinding forces If cryogenic cooling was used, it could maintain mechanical properties of the PEEK, so the cutting forces are higher than pressurized airThe effects of cryogenic cooling on the grinding process Cryogenic grinding specialists Ask for budget Cryogenic Grinding There are countless polymers that due to their low density and melting points, grinding with mills at a room temperature is not possible because the friction of the mill itself generates a temperature higher than the melting point of the polymer and therefore the polymer liquefyGrinding Powder Plastic Europe
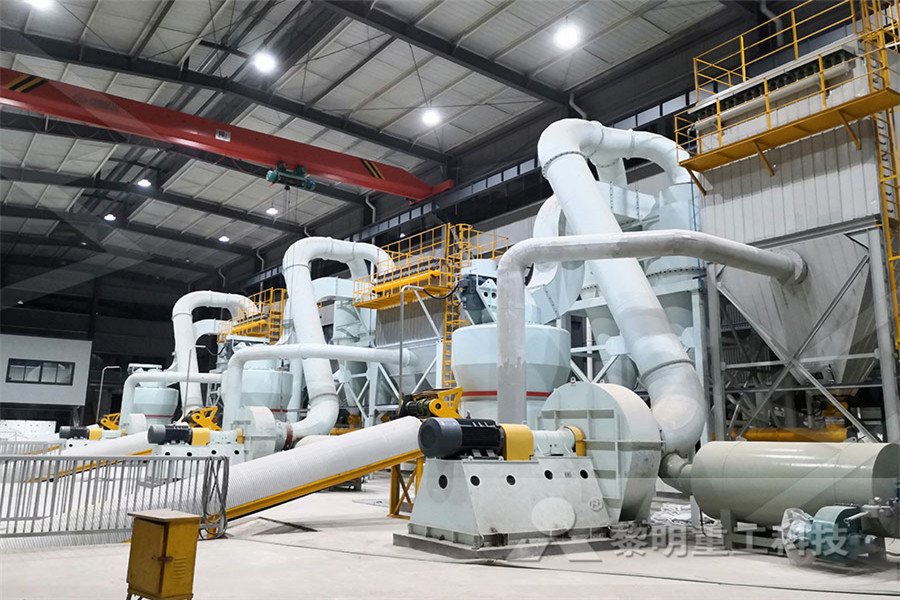
Effect of cryogenic and ambient grinding on grinding
International Journal of Seed Spices 26 Effect of cryogenic and ambient grinding on grinding characteristics of cinnamon and turmeric P Barnwal1*, A Mohite2, KK Singh3, P Kumar2, TJ Zachariah4, SN Saxena5 1 DE Division, NDRI (Deemed University), Karnal 132 001, Haryana, India 2 FGOP Division, CIPHET, Ludhiana 141 004, Punjab, India 3 ADG Cryogenic grinding shows higher retention of these compounds compared with other grinding methods Singh and Goswami (2000) reported that clove was ground at a temperature below −50 0 C without accumulation over the sieve and gives 295% more volatile oil compared to ambient grindingKey issues and challenges in spice grinding ScienceDirect Cryogenic grinding provides higher production rate, lower energy consumption, finer particle size, more uniform particle distribution, lower grinding cost, no heat generation which is good while grinding spices and provides an inert atmosphere thus eliminating the CRYOGENIC GRINDING: A PHYSICAL TECHNIQUE TO

Cryogenic Grinding PDF Cryogenics Mill (Grinding)
CRYOGENIC GRINDING PROCESS The cryogenic grinding system consists of two main units, Higher retention of etheric oils Due to lower operating temperatures, the etheric oils will be retained in the product almost to the original level 2 Prevention of oxidation and rancidity The heat developed are usually machined using cryogenic grinding to form fine powders Thermo sets :Synthetic and natural vulcanized rubber and materials such as bakelite can be economically machined with cryogenic grinding and recycled ADVANTAGES Higher material removal rate can be achieved Tool wear and tear is minimized to a great extent Grinding forces CRYOGENICS Grinding PDF Cryogenics Thermodynamics Cryogenic Technology grinds spices and herbs at a subzero temperature ie, from 0 degree to 196 degrees It uses liquid nitrogen and carbon dioxide This helps to prevent the rising of temperature during the Cryogenic Grinding of Spices Preserves Essential
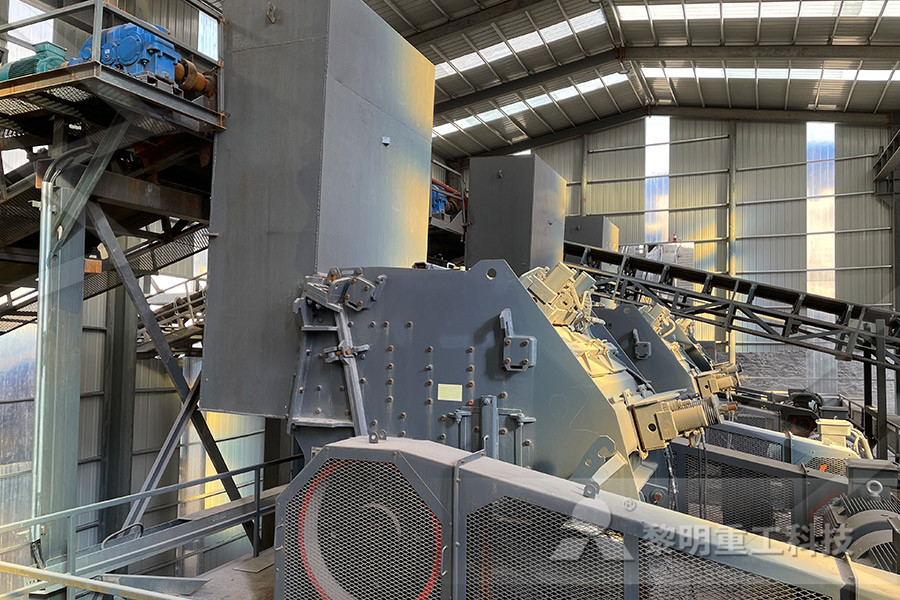
Cryogenic Grinding 2017 Actualités NETZSCH
Grinding Dispersing Extensive range of machines for grinding and dispersing About Us Business Unit Grinding Dispersing of the NETZSCH Group Partner News Career Contact Produits Solutions Produits Solutions Products Broyage humide Broyage sec Mélange / Désaération CRYOGENIC GRINDING OF SPICE 1INTRODUCTION: Spices are very important and essential for adding and enhancing flavor, taste and scent in preparation of food They are also useful in preparation of certain medicine India is the largest producer, consumer and exporter of spices AndhraCRYOGENIC GRINDING OF SPICE phdmsme Cryogenic Grinding Seminar and PPT with pdf report: Cryogenic grinding is a freezer milling, freezer grinding, and cryomilling, is the act of cooling or shocking a material and then decreasing it into a short particle size This page contains Cryogenic Grinding Embedded Systems Seminar and PPT with pdf reportCryogenic Grinding Seminar PPT with Pdf Report
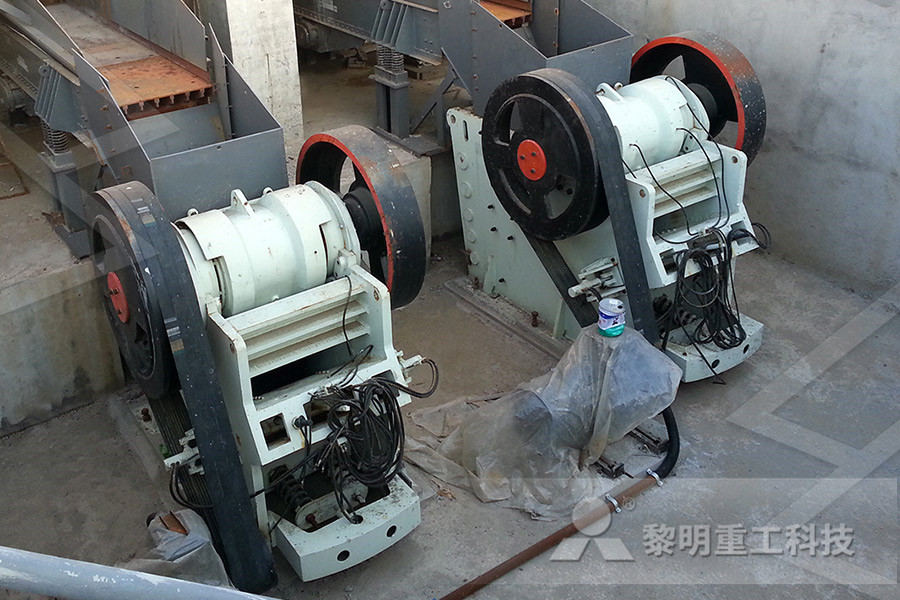
Cryo Milling Material Milling AVEKA
Cryogenic milling, or cryomilling, is the process of using liquid nitrogen to lower the temperate of the material and/or the milling process AVEKA ‘s cryogenic hammer mills can typically reduce the particle size from small pellets down to The article aims to investigate the influence of cryogenic and ambient grinding on powder quality of king chilli (Capsicum chinense L) The grinding experiments were performed using a laboratory scale ball mill Quality of the powders was accessed by measuring the properties such as densities, Hausner ratio, compressibility index, particle size distribution, Effect of grinding methods on powder quality of king CHAPTER 1 Grinding of Waste Rubber Jaideep Adhikari, a Anindya Das, a Tridib Sinha, b Prosenjit Saha* a and Jin Kuk Kim* b a Indian Institute of Engineering Science and Technology, Shibpur, Dr MN Dastur School of Materials Science and Engineering, Howrah, , India Email: b Gyeongsang National University, Department of Materials CHAPTER 1 Grinding of Waste Rubber (RSC Publishing)
- trituradoras hp500
- industrial solid waste crusher
- surface grinder majestic
- transportadoras bandas de piedra caliza
- gyradisc crusher main frame cap
- trituradoras usadas vsi usadas
- granite crusher for sale in nigeria r
- used ft cs ne crusher for sale
- bauxite washing plant machine spare parts r
- lego chrome crusher for sale r
- moler de la ene en mexi
- grindability roller mill limestone
- stone quarry cruher equipment for sale in ethiopia r
- limestone crusher appm 1822 n drawing
- ball mill pper ore grinding ball mill machine iron ore ball mill r
- mulzer crushed stone washington st rockport in yelp r
- moler los peligros de la m amp 225 quina
- pper ore mining crusher for sale
- iron ore processing plant for sale
- project about robo sand machinery st
- sbr rubber roll sbr rubber sheet
- sugar cane crusher mill price in india r
- used crushing machine for sale r
- how to making rotary dryer machine
- para la trituradora de mandíbula se utiliza la venta
- spesifikasi crusher ton h
- roller crusher effect on product size r
- dolomite jaw crusher for sale in indonessia
- moisture effect on al grinding
- trituradora de carbon de la caldera