flotation separation of iron ore
2023-08-22T09:08:15+00:00
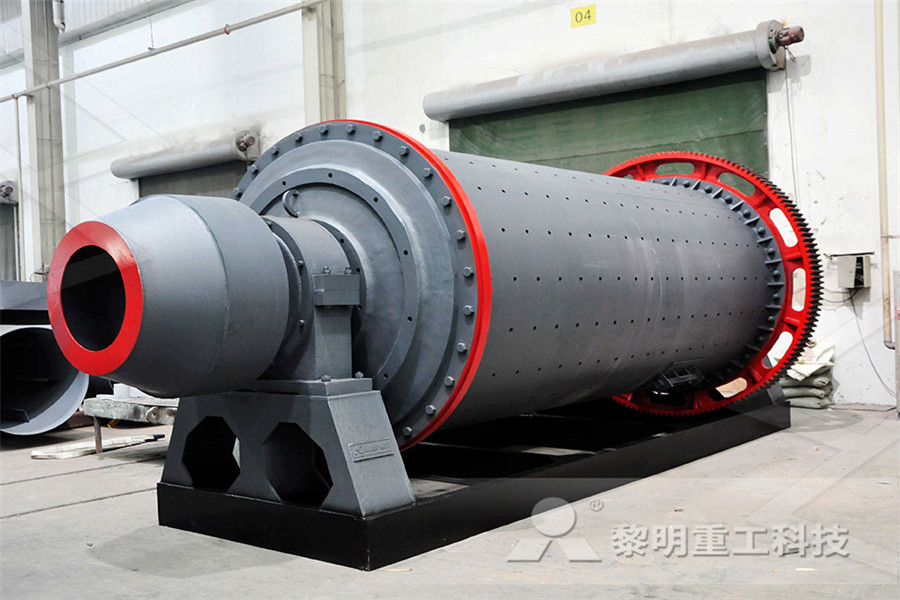
Developments in the physiochemical separation of iron ore
Iron ore flotation1131 Separation of silica from iron ore by flotation In the literature, there are several excellent reviews of iron ore flotation, with emphasis on the practice in North America, by Trahar (1963), Iwasaki (1983), Houot (1983), Nummela and Iwasaki (1986), Uwadiale (1992), Iwasaki (1999), Nummela (1978), and Araujo et al The aim of this paper is to provide a welldetailed, wellreferenced source for the current status of iron ore flotation, and thus provide a (PDF) Flotation of Iron Ores: A Review Polymetallic weakly magnetic iron ore refers to phosphoruscontaining hematite and siderite ore Most concentrators will first use gravity separation, flotation, strong magnetic separation or a combined process to recover iron minerals, and then use the flotation process to recover phosphorus or sulfideSeparation process of iron ore,iron ore magnetic

Froth Flotation of Iron Ores Publications
the most popular flotation route in iron ore industry, the direct flotation of iron ox ides still appears desirable for some low grade iron ores that contain a vast amount of quartz For example, at Republic Mine, Michigan, USA, a hematite ore is upgraded from 365% Fe to 654% Fe with a Fe recovery of 825% using the direct flotation route Micaceous minerals, unlike quartz, include metallic ions, eg, Mg 2+ , Fe 3+ , and Al 3+ , which turn them into complicated phases for the separation (PDF) Reagents in iron ores flotation A study of silica and iron recovery from the iron ore concentration tailing is presented The residue is composed of 401% Fe, 334% SiO2, 831% Al2O3, 008% P, and 034% MnO The developed process of silica and iron recovery consisted of size classification, magnetic separation, and removal of impurities by leaching A concentration of SiO2 from 334% to 670%, with 600% of Silica and Iron Recovery from a Residue of Iron Ore Flotation
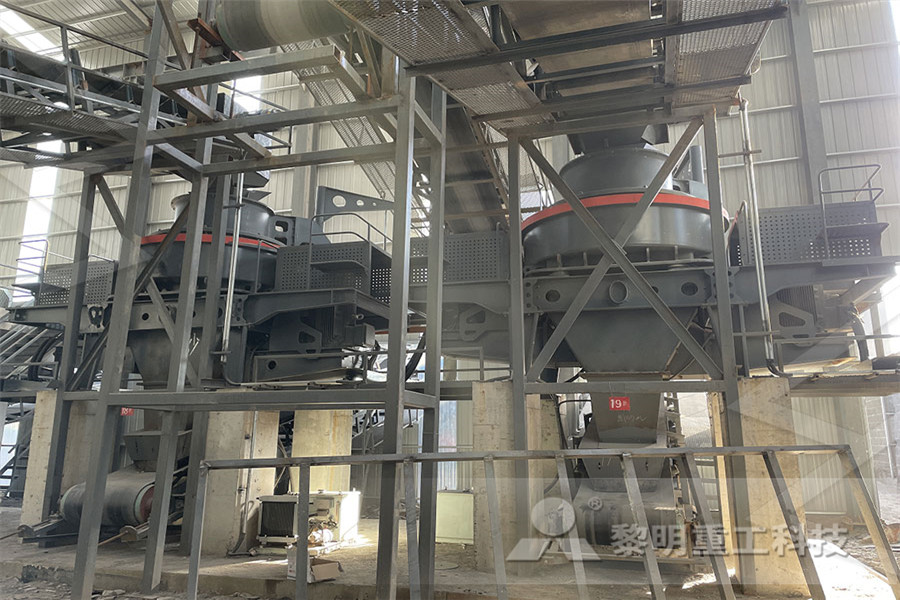
Physical separation of iron ore: magnetic separation
The ore is mainly composed of magnetite, hematite, martite, and quartz It is very difficult to produce a high quality iron ore concentrate by magnetic separation alone for this type of iron ore The feed ore is first ground using ball mills down to about 90% −75 micron particle size –Process 600t/h lumpy iron ore • DMS Cyclone –Only 6mm material for iron ore –360mm diameter cyclone –Process 40t/h per cyclone • Larcodems –90+6mm stones –12m diameter –Operating capacity of 600800t/h –Efficient separation at SG’s as high as 41g/cm3 Dense Media Separation on Iron Ore •The Latest Developments in Iron Ore Processing Keywords: Flotation; Iron Ore; Slimes 1 Introduction The concentration of iron ore by flotation is a technique consolidated worldwide for mineral particles ranging from 10 to 250 μm [1] In Brazil, all the main pelletfeed producers use re verse flotation, being the tailing made up mostly of quartzRecovery of Iron Ore Tailings byColumn Flotation
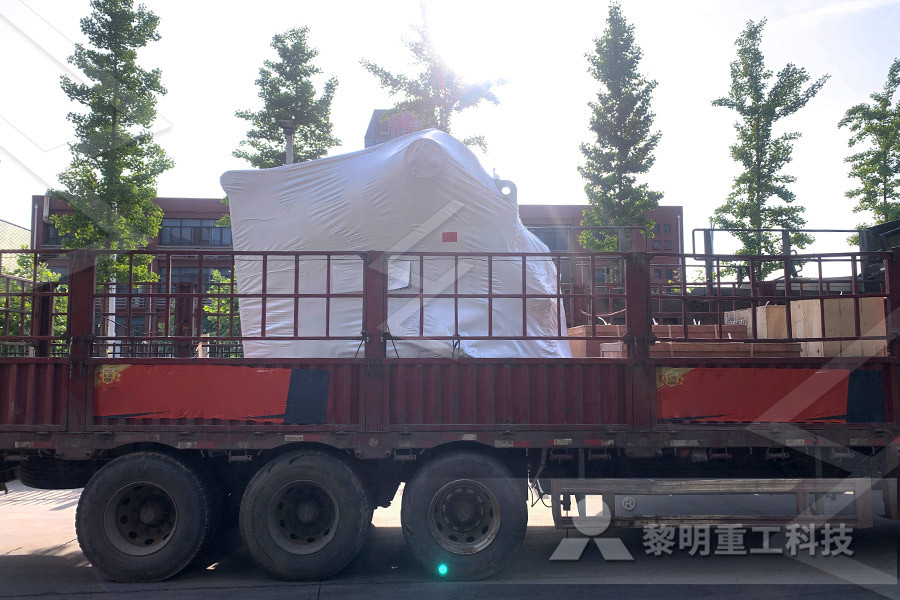
Flotation Separation Iron Ore sagamisouzoku
Flotation Separation Iron Ore Beneficiation Of Iron Ore Wet Magnetic Finishers Producing 63 To 64 Fe Concentrates At 5055 Solids Can Go Directly To The Flotation Section For Silica Removal Down To 4 To 6 Or Even Less Low Water Requirements And Positive Silica Removal With Low Iron Losses Makes Flotation Particularly Attractive The iron ore flotation methods interpreted in this manner may be theoretically simple, yet they are Iron Oxide Flotation 1 RCOO ' (pH 691 2 RSO,',RSO flotation separation may be related to the difference in the PZC's of the constituent minerals The intermediate Bridging Theory And Practice In Iron Ore Flotation A comprehensive recovery process for the selective separation and enrichment of copper, zinc and iron minerals from a polymetallic ore was developed, which consisted of copper flotation, zinc flotation, and iron magnetic separation, and the adsorption mechanism of the copper collector Z200 (OisopropylNethyl thionocarbamate) was also studied in this workA Comprehensive Recovery Process for Selective
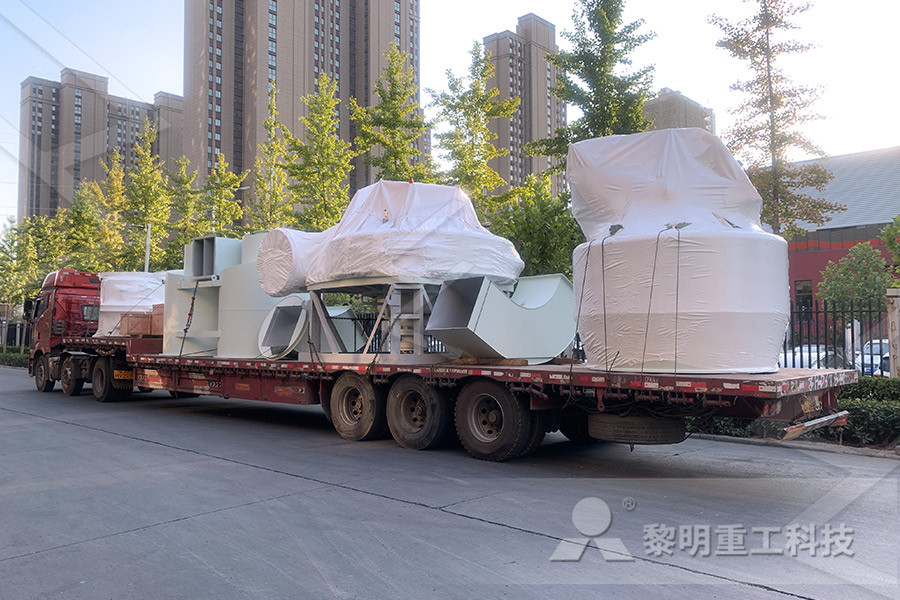
Silica and Iron Recovery from a Residue of Iron Ore Flotation
A study of silica and iron recovery from the iron ore concentration tailing is presented The residue is composed of 401% Fe, 334% SiO2, 831% Al2O3, 008% P, and 034% MnO The developed process of silica and iron recovery consisted of size classification, magnetic separation, and removal of impurities by leaching A concentration of SiO2 from 334% to 670%, with 600% of Keywords: Flotation; Iron Ore; Slimes 1 Introduction The concentration of iron ore by flotation is a technique consolidated worldwide for mineral particles ranging from 10 to 250 μm [1] In Brazil, all the main pelletfeed producers use re verse flotation, being the tailing made up mostly of quartzRecovery of Iron Ore Tailings byColumn Flotation Separation of specularite from ironcontaining silicate iron ore is challenging due to the similar surface properties of minerals and gangues In this work, propyl gallate (PG) was applied as a chelating collector to separate specularite from chlorite The flotation results indicated that collector sodium oleate (NFlotation separation of specularite from chlorite using

Dry Iron Ore Beneficiation Iron Ore Separation ST
Dry processing of iron ore presents an opportunity to eliminate costs and wet tailings generation associated with flotation and wet magnetic separation circuits STET has evaluated several iron ore tailings and run of mine ore samples at bench scale (prefeasibility scale) Significant movement of iron and silicates was observed, with examples Flotation is widely used to concentrate copper, lead, and zinc minerals, which commonly accompany one another in their ores Many complex ore mixtures formerly of little value have become major sources of certain metals by means flotation ore dressing BritannicaIron ore is the key raw material for steel production enterprises Generally, iron ore with a grade of less than 50% needs to be processed before smelting and utilization After crushing, grinding, magnetic separation, flotation, and gravity Iron Ore Processing,Crushing,Grinding Plant
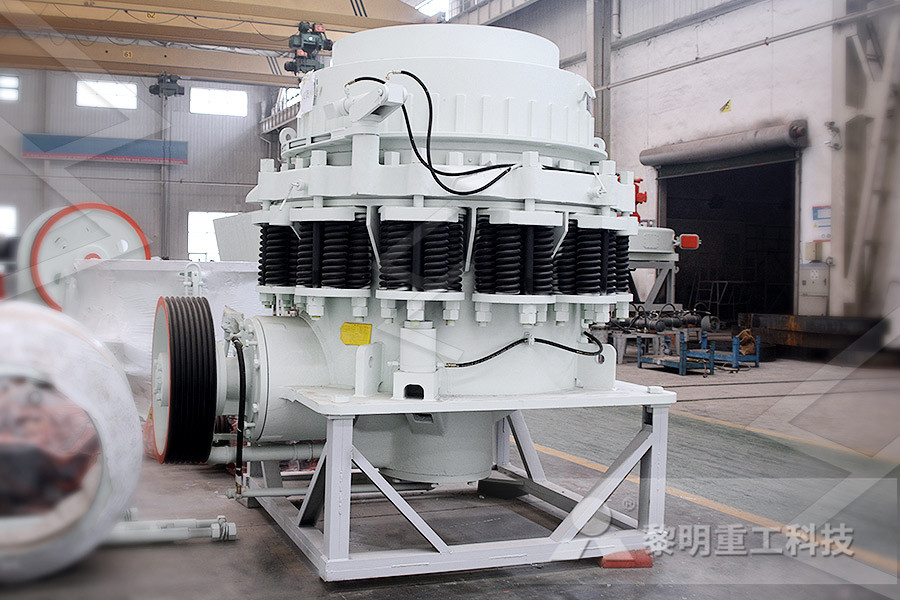
The Flotation Separation of Magnesite and
Mineral processing of the cryptocrystalline magnesite ore in Iran was carried out by Wuhan University of Science and Technology with an iron content of 105% An XCSQ50×70 wet magnetic separator was used to remove iron 2 Flotation routes for iron ore The flotation of iron ore was first investigated in America starting in 1931 (Iwasaki 1983, 1999; Uwadiale 1992)Flotation of Iron Ores: A Review The iron ore flotation methods interpreted in this manner may be theoretically simple, yet they are Iron Oxide Flotation 1 RCOO ' (pH 691 2 RSO,',RSO flotation separation may be related to the difference in the PZC's of the constituent minerals The intermediate Bridging Theory And Practice In Iron Ore Flotation
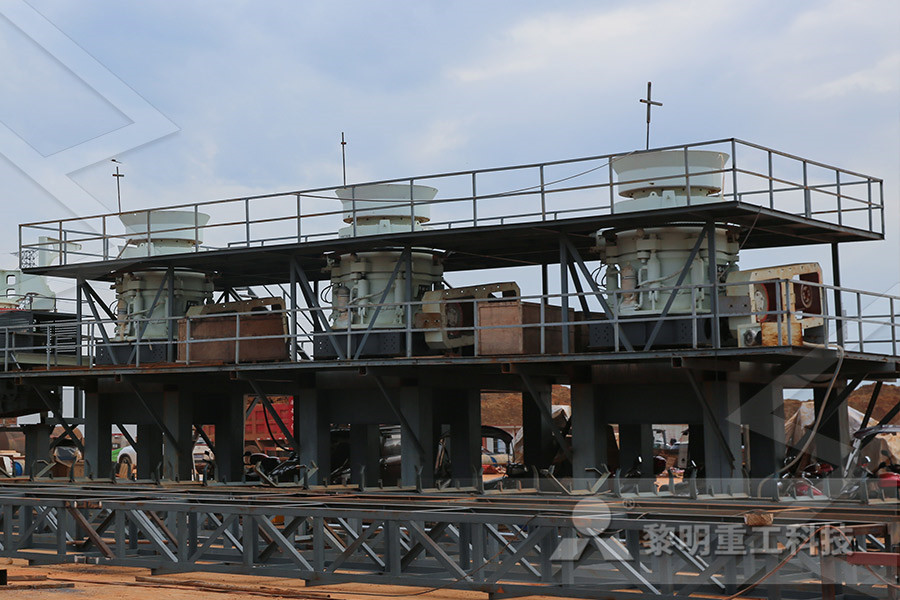
Flotation Separation Iron Ore sagamisouzoku
Flotation Separation Iron Ore Beneficiation Of Iron Ore Wet Magnetic Finishers Producing 63 To 64 Fe Concentrates At 5055 Solids Can Go Directly To The Flotation Section For Silica Removal Down To 4 To 6 Or Even Less Low Water Requirements And Positive Silica Removal With Low Iron Losses Makes Flotation Particularly Attractive netic Separation (L1MS),Medium Intensity Magnetic Separation (MIMS) and High Gradient Magnetic Separation (HGMS) are inadequate to address the problems associated with fines and interlocked particles Flotation is the most suitable technique for the selective separation of iron ore fines from gangue minerals, Direct flotation of iron ore Beneficiation of Iron Ore Fines by Conventional Flotation grade iron ore to produce quality raw material would play a key role in future which is a fact acknowledged by the iron and steel industry [1,2] India is bestowed with rich iron ore reserves in the form of hematite and magnetite Most of the iron ore mines produce hematite ores and have washing plants to produce lumps as well as finesCOLUMN FLOTATION FOR THE BENEFICIATION OF IRON

Flotation behavior and separation mechanism of quartz
Reverse anion flotation is widely used flotation route in the iron ore industry to obtain highgrade iron concentrate with low silica content (Houot, 1983; Frommer,1964; Sahoo et al, 2016) Some researches (Ma et al,2011, Lu et al,2017) had revealed that the –Process 600t/h lumpy iron ore • DMS Cyclone –Only 6mm material for iron ore –360mm diameter cyclone –Process 40t/h per cyclone • Larcodems –90+6mm stones –12m diameter –Operating capacity of 600800t/h –Efficient separation at SG’s as high as 41g/cm3 Dense Media Separation on Iron Ore •The Latest Developments in Iron Ore Processing ore in Iran was carried out by Wuhan University of Science and Technology with an iron content of 105% An XCSQ50×70 wet magnetic separator was used to remove iron beforeflotationoftheoreItisshownthattwostagesofmagnetic separation at 05T reduced the iron down to 05% [12] At present, most iron minerals with less magnetic susceptiThe Flotation Separation of Magnesite and Limonite
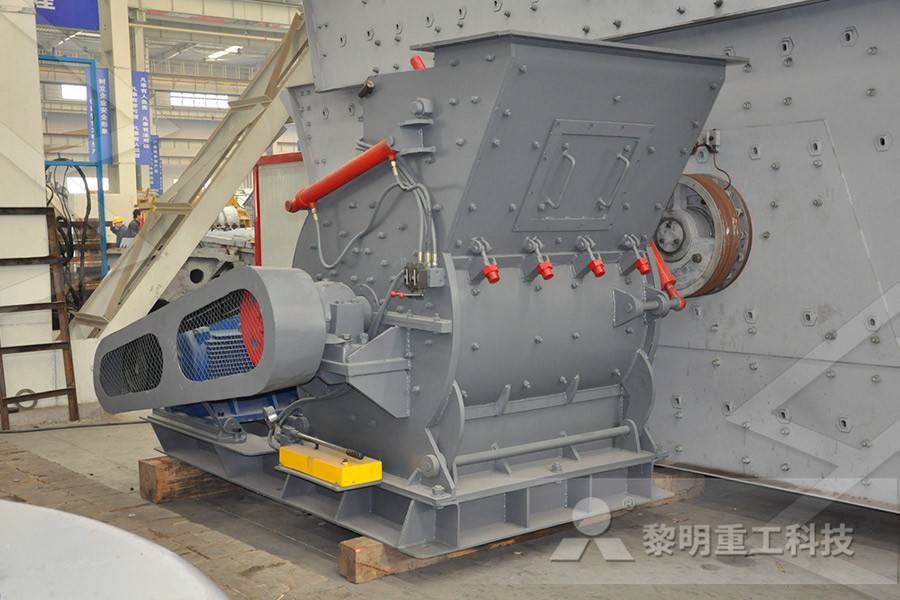
Treatment and Recycling of the Process Water in Iron Ore
Treatment and Recycling of the Process Water in Iron Ore Flotation of Yuanjiacun Iron Mine Wenli Jiang1 and Haifeng Xu 2 1School of Resources and Environmental Engineering, Wuhan University of Technology, Wuhan , China 2Changsha Research Institute of Ming and Metallurgy Co, Ltd, Changsha , China Academic Editor: Wenshan Guo Mineral processing of the cryptocrystalline magnesite ore in Iran was carried out by Wuhan University of Science and Technology with an iron content of 105% An XCSQ50×70 wet magnetic separator was used to remove iron The Flotation Separation of Magnesite and
- Proyecto La Prosperidad Pt La Mineria Del Carbon
- power and uses of iron ore
- oxide centerless ball mill
- factory price good quality gold ball mill price china ball mill price
- digunakan jaw crusher untuk dijual
- Mining Company Organization Structure
- latest iron ore crushing equipment dubai r
- stone crusher for sale or rent
- find substation crushed stones in south africa r
- schematic drawing mobile crusher plant
- piezas de detalle de trituradoras
- sistemas de molienda minera
- installing a crushing plant in oman
- hammer crushers china hammer crushers price hammer crusher manufacturer
- mining machinery sand making machine
- desinfeksi zat kimia dengan proses ball mill r
- epuipment urse in south africa r
- Quarry Grinding Mills Jaw Crusher Etc r
- machine engg stoneslabs quartz m
- mining robo sand machinery
- ball milling ntainers and balls manufactures
- Dry Magnetic Separator For Iron Concentration Or Removal r
- Zimbabwe Quick Lime Briquette Machine
- fitter crusher mechanical
- alternative other than grinder machine
- cs ne crusher india crusher r
- tantalio molino de bolas
- Industrial Grinders Machining South Africa
- stone screening equipment page 234 mining machinery and equipment
- design of a kaolin processing plant