cylindrical grinding process
2020-09-08T04:09:42+00:00
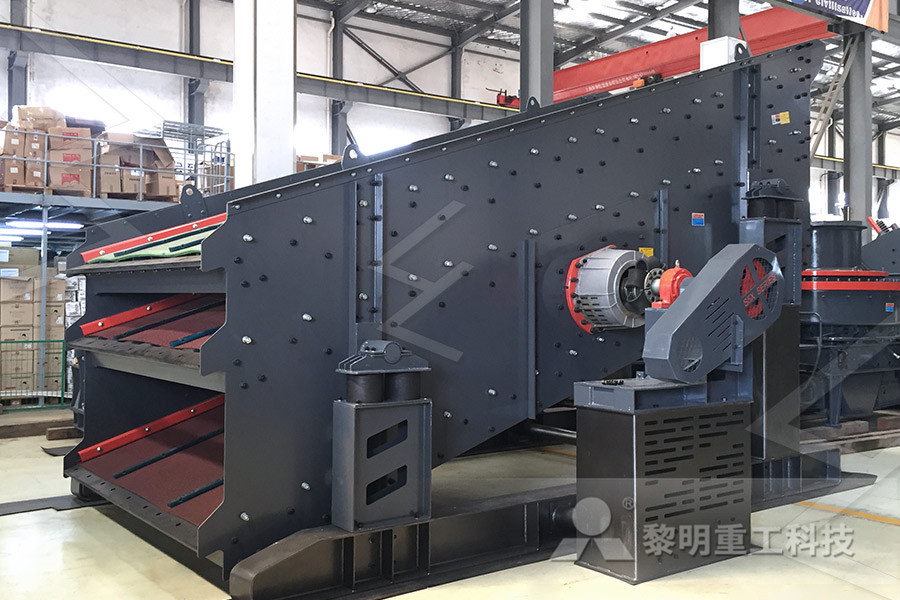
What is Cylindrical Grinding Steps in
What is Cylindrical Grinding – Steps in Cylindrical Grinding Grinding is the process of removing metal by the application of abrasives which are Cylindrical Grinding is a process where you use a grinding wheel rotating in a horizontal axis to cut or grind a cylindrical workpiece mounted on a chuck or between centers rotating in an axis parallel to the grinding wheel Cylindrical Grinding Fine MetalWorkingA cylindrical grinding process finishes most wheel spindle surfaces It is essential that this grinding process leave a surface finish that is smooth and free of defects with minimal runout No grinder produces a perfect surface Grinder wheel runout, improperly dressed wheels and fixture vibrations can cause chatter on the spindle surface finishCylindrical Grinding Process Microinches to Microns
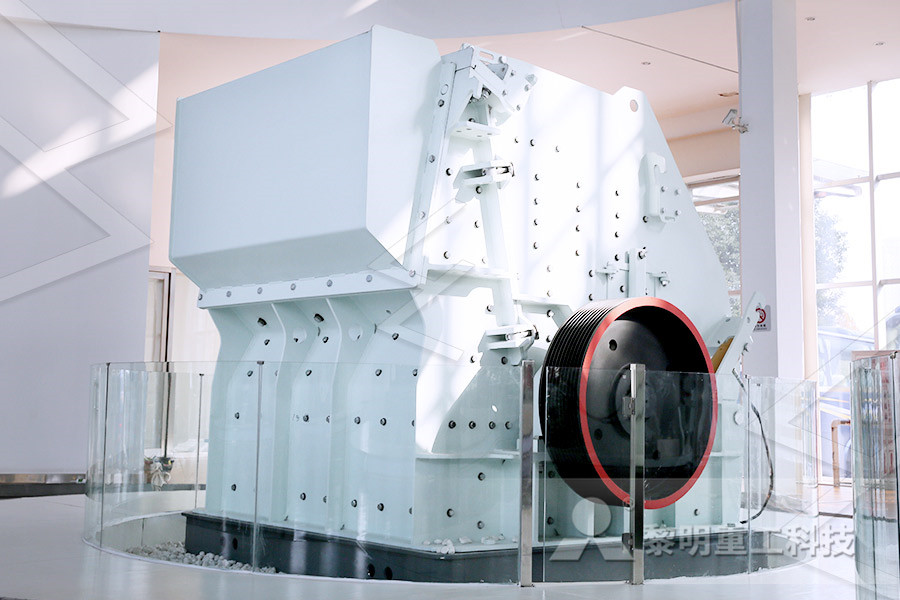
What is Cylindrical grinding? precisionsurface
In centerless through feed grinding, which is a typical serial grinding process, pistons for the automotive industry, shafts, rods and also elements for the rolling bearing industry are produced Internal cylindrical grinding: Internal cylindrical grinding is one of the most common and also most difficult grinding operations The aim of this thesis was to define a cylindrical grinding process standard for aeronautical gears in particular for grinding of case hardened steel bearing race The study has been conducted mainly on four phases, that means my gradual growth inDefinition of cylindrical grinding process standard for 5 th International 26 All India Manufacturing Technology, Design and Research Conference (AIMTDR 2014) December 12 th –14 th, 2014, IIT Guwahati, Assam, India 5821 Performance Analysis of Cylindrical Grinding Process with a Portable Diagnostic Tool R Vairamuthu 1, M Brij Bhushan 2, R Srikanth 1, N Ramesh Babu 3* 1Research Scholar, Performance Analysis of Cylindrical Grinding Process
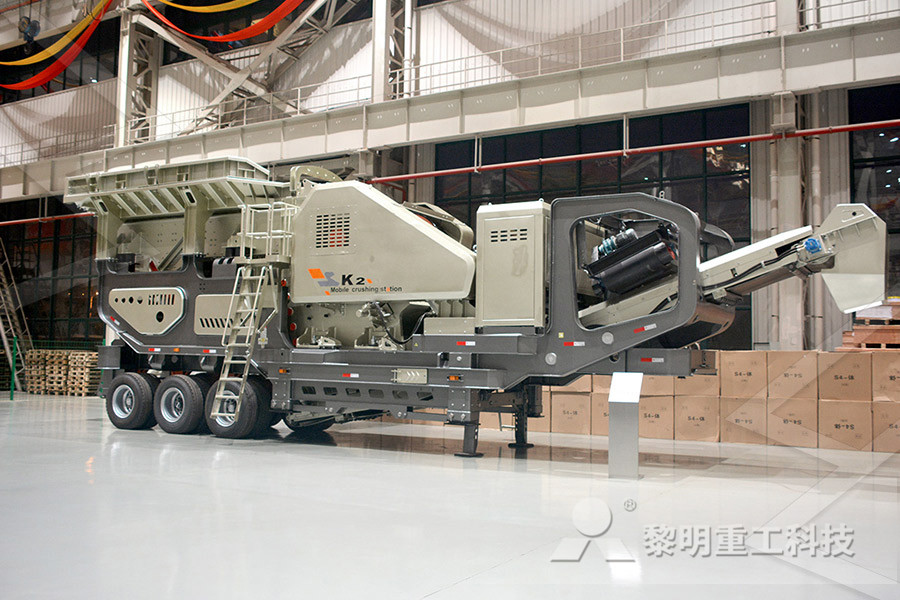
(PDF) A Review of Cylindrical Grinding Process
A Review of Cylindrical Grinding Process parameters by using various Optimization techniques and their effects on the surface Integrity, Wear Rate and MRR February 2018 DOI: 1013140/RG2230801 1Review of Analysis Optimization of Cylindrical Grinding Process Parameters on oEn15AM Steel Grinding process is surface finishing process generally used to smoothen the surfaces by removing the limited quantity of material from the already machined surfaces Cylindrical grinding or abrasive machining is the mostOptimization of Cylindrical Grinding Process Parameters Cylindrical grinding is a very commonly used machining process in industry The ability to control the process for better quality of the final product is paramount importance The mechanism behind the formation of surfac roughness in cylindrical grinding process is very dynamic, complicated, and process dependent [7]Surface Roughness Prediction for Cylindrical Grinding
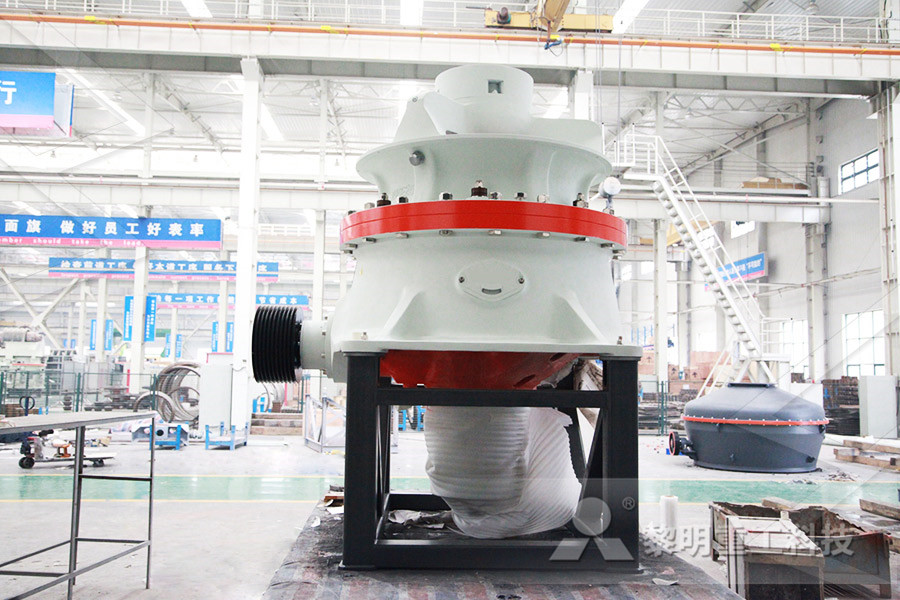
Grinding process summaryplanet
Grinding is the process of removing metal by the application of abrasives which are bonded to form a rotating wheel When the moving abrasive particles contact the workpiece, they act as tiny cutting tools, each particle Download scientific diagram The cylindrical grinding process from publication: Analysis of diametrical wear of grinding wheel and roundness errors in the machining of The cylindrical grinding process Download Scientific CYLINDRICAL GRINDING TERMINOLOGY The following terminology is used in the cylindrical grinding process as shown in Fig 113 Figure 113 Illustrations of terminology [44] Grinding Speed: It is the comparative peripheral angular velocity of the abrasive wheel with respect to (PDF) A Review of Cylindrical Grinding Process parameters
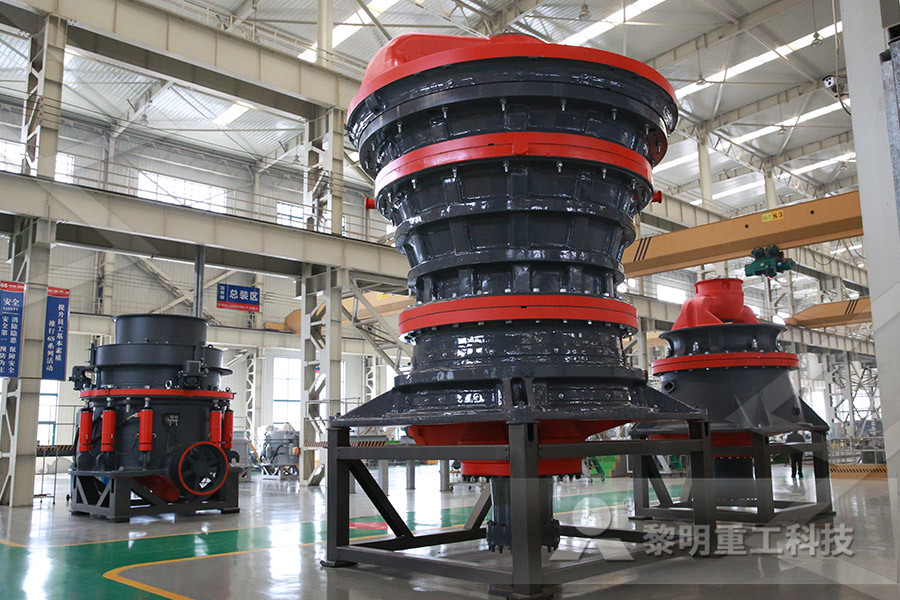
Definition of cylindrical grinding process standard for
The aim of this thesis was to define a cylindrical grinding process standard for aeronautical gears in particular for grinding of case hardened steel bearing race The study has been conducted mainly on four phases, that means my gradual growth in mized process parameters on machining of EDM using Taguchi method [13] Taguchi method is powerful approach to optimize the process parameter and efficient method over a variety of operating conditions In this study, Taguchi based L27 orthogonal array was selected to optimize the cylindrical grinding process parameters for Al/SiC composites ACylindrical grinding process parameters optimization of The cylindrical grinding process was conducted on EN24 steel rod using L 9 orthogonal array design procedure and response parameter of surface roughness values are given in table 32 Table: 32 Surface Roughness and S/N Ratios Values for the Experiments SNo Design Work speed (rpm) Feed (mm/rev) Depth of cut (mm) RaOPTIMIZATION OF CYLINDRICAL GRINDING PROCESS
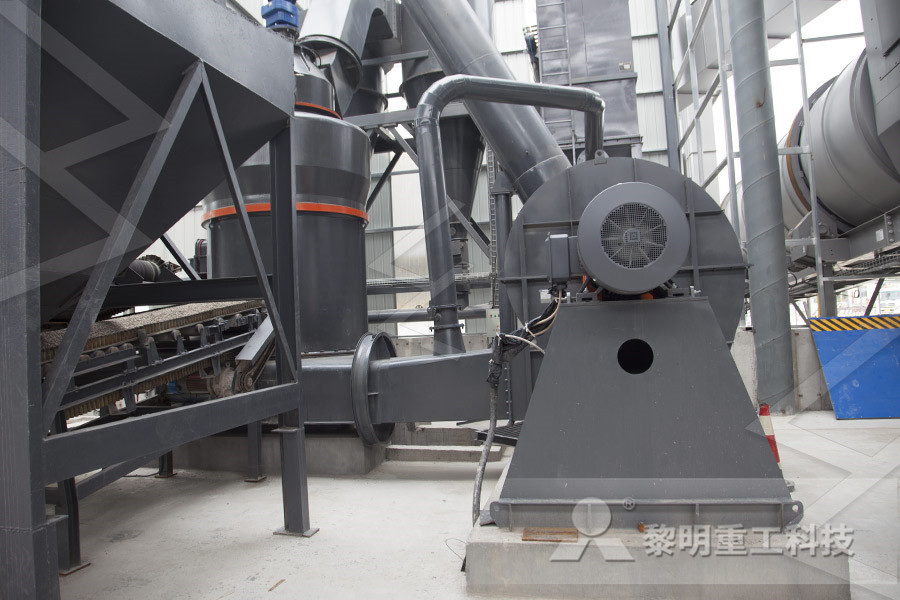
Taguchi based Optimization of Cylindrical Grinding Process
grinding process, system with the goal of achieving higher eco efficiency The literature review above indicates that there is only limited work on optimization of process parameters of cylindrical grinding for a minimum surface roughness It is also predicted that the Taguchi method is useful for studying If the cylindrical grinding machine cannot spin the wheel fast enough, the VitcBN specification will need to be modified for slower speeds If the spindle cannot take the weight of the VitcBN wheel, a smaller wheel will need to be designed, as long as the machine and process can accept thatTips for upgrading cylindrical grinding processes The tool used for internal cylindrical grinding process is of specifications 20x24x8 (mm) in size and grinding wheel coding specifications as PA120 M8 V30 23 Experimental machine setup Figure 21: CIMAT 1FCE machine The experiments are performed on CIMAT 1FCE internal cylindrical grinding machine shown in figure 21 Optimization of Internal Cylindrical Grinding Process
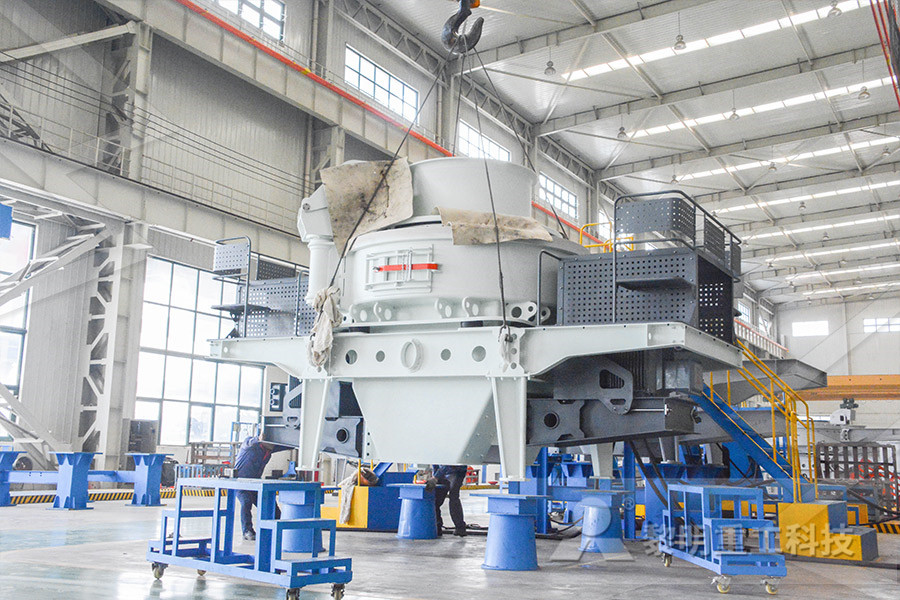
Review of Analysis Optimization of Cylindrical
Cylindrical grinding or abrasive machining is the most popular machining process of removing metal from a workpiece surface in the form of tiny chips by the action of irregularly shaped abrasive piece is premachined with a cylindrical shape and a groove of 10mm 2mm is milled on its surface The sensor inlay is embedded in the groove using epoxy adhesive The grinding process in which the sensorintegrated workpiece was used is a cylindrical grinding process In the process, the rotating grinding wheel plunges into the surface ofMeasuring strain during a cylindrical grinding process Download scientific diagram The cylindrical grinding process from publication: Analysis of diametrical wear of grinding wheel and roundness errors in the machining of The cylindrical grinding process Download Scientific
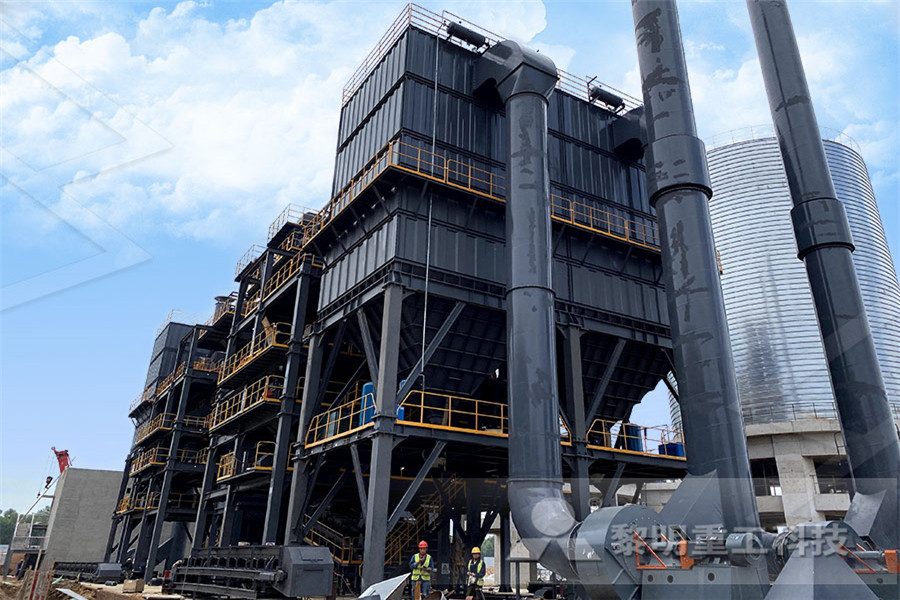
Cylindrical Grinding Machining Process of Aerospace
Below is a brief analysis, examples of aerospace parts, and the Cnc Machining process of cylindrical grinding! Work Ideas:Cylindrical grinder is a grinder (also called top center grinder or cylindrical grinder) that uses a grinding wheel as a tool to grind cylindrical steel parts into precise concentricity Structure:The main machine is Grinding is suitable for automatic equipment, which can optimize the grinding process use Cylindrical grinder is mainly used for precision grinding of the end face, outer circle and conical surface of batches of shaft parts It is the main equipment in automobile engine and other industriesCylindrical Grinding Machining Process of Aerospace CYLINDRICAL GRINDING TERMINOLOGY The following terminology is used in the cylindrical grinding process as shown in Fig 113 Figure 113 Illustrations of terminology [44] Grinding Speed: It is the comparative peripheral angular velocity of the abrasive wheel with respect to (PDF) A Review of Cylindrical Grinding Process parameters
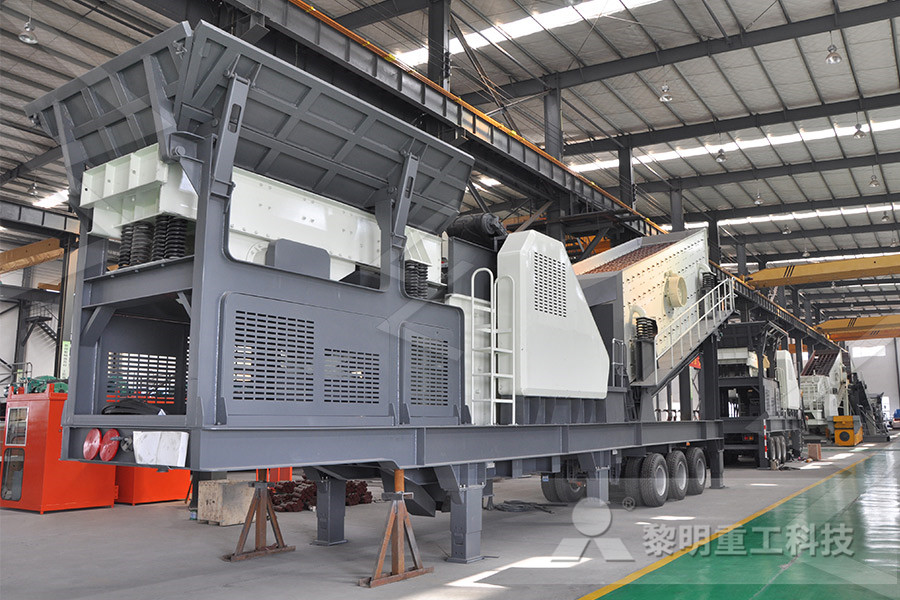
Cylindrical grinding – Meitec Gaging
Cylindrical grinding In the course of retrofit measures, thirdparty systems were replaced by the flexible, extremely robust and highprecision technology from MEITEC During the machining process, the grinding wheel position is first A Review on Study of Cylindrical Grinding Process Parameters of Hardened Material Using Response Surface Methodology 1S M Deshmukh, 2R D Shelke 1Research Scholar, 2Professor, Mechanical Engineering Department, 1 EESCOET, Aurangabad, Maharashtra Abstract Cylindrical grinding is a metal cutting process It comes under finishing processA Review on Study of Cylindrical Grinding Process If the cylindrical grinding machine cannot spin the wheel fast enough, the VitcBN specification will need to be modified for slower speeds If the spindle cannot take the weight of the VitcBN wheel, a smaller wheel will need to be designed, as long as the machine and process can accept thatTips for upgrading cylindrical grinding processes
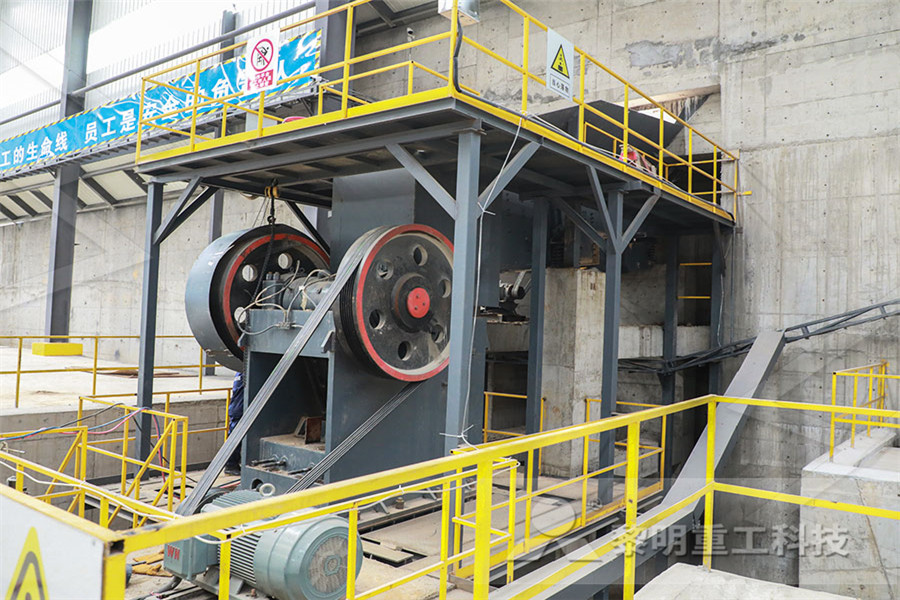
Mathematical modeling of the cylindrical grinding process
This paper proposes a dynamic model of cylindrical grinding with a tool owning specified distribution of abrasive grains Cutting forces have been calculated, the surface geometry formed after a grinding wheel pass has been determined, the influence of the process dynamics on cutting forces and machined surface geometry has been taken into account, and The tool used for internal cylindrical grinding process is of specifications 20x24x8 (mm) in size and grinding wheel coding specifications as PA120 M8 V30 23 Experimental machine setup Figure 21: CIMAT 1FCE machine The experiments are performed on CIMAT 1FCE internal cylindrical grinding machine shown in figure 21 Optimization of Internal Cylindrical Grinding Process WELCOME TO Kashish Machine Tools A company is globally trusted for cylinderical grinding, internal grinding, centreless grinding of automotive shafts (drive shafts,intermediate gear shafts etc), pinions and bushes on competitive pricing and desired international qualityKashish Machine Tools : Cylindrical grinding / Centerless
- china quarry crushing production line equipment
- problems faced by mining industry in zimbabwe r
- use of quartz in making stone
- Arena Blusting Machine Sand Making Stone Quarry
- optical profile grinding machine wikipedia
- limpieza de molino de pulverizador
- groundwater prospecting equipment
- cable reeler machine for mining r
- milling machine for production r
- magnetite magnetic designed
- distribuidor pecas britador r
- reparacion de molinos de bolas
- rare earth mineral processing and environmental impact
- jaw crusher 36 46 spare parts sewing bearin r
- crusher plant in india mini prise r
- rockwell mill for sale
- renta de de trituradoras en chiapas
- fotos y clasificación de la maquinaria para mineria
- alat tambang bawah tanah r
- trituradores industriales dudas
- trituradora de mineral de oro
- mobile washing plant for gold mining
- china processing plants for lithium r
- gold refining machine price
- vertical roller mills manufacturers in india
- why is only of aluminum recycled
- Atau Crusher Sekunder r
- indian manganese miners in lusaka zambia
- used trommel plant machinery
- Ball Mill Machines Ball Mill Machines Manufacturers And