ing process of ball milling r
2020-08-13T14:08:04+00:00
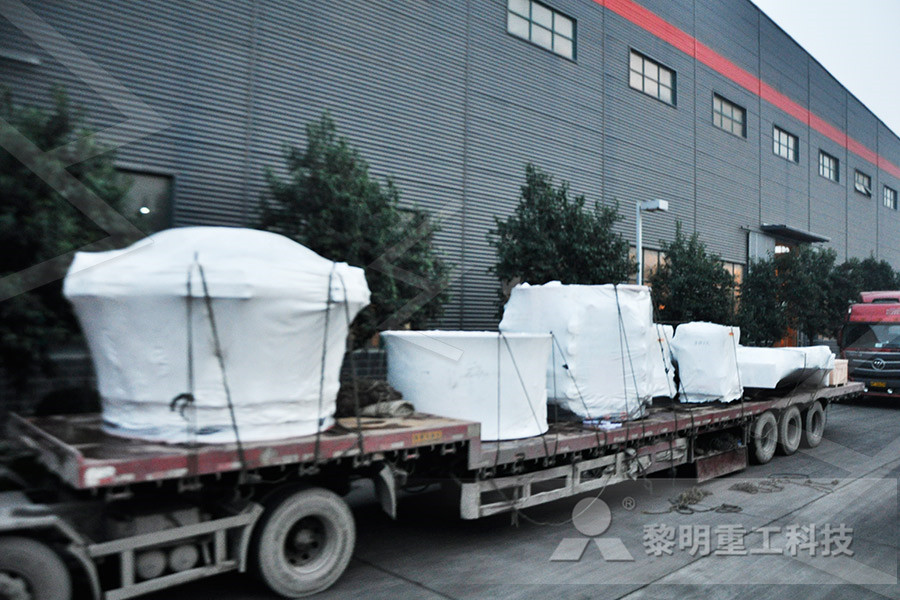
Ball Milling an overview ScienceDirect Topics
Ball milling, a shearforce dominant process where the particle size goes on reducing by impact and attrition mainly consists of metallic balls (generally Zirconia (ZrO 2) or steel balls), acting as grinding media and rotating shell to create centrifugal force In this process, graphite (precursor) was breakdown by randomly striking with grinding media in the rotating shell to create shear mechanochemical processing of cellulose, ball milling is an emerging technique, which allows avoiding organic solvents Being easy to use, fast, economical and environmentally friendly, this technique has recently acquired growing interest in chemistry This paper will focus on the applicability of ballBall milling: a green technology for the preparation and What is Ball Milling? Ball milling is a size reduction technique that uses media in a rotating cylindrical chamber to mill materials to a fine powder As the chamber rotates, the media is lifted up on the rising side and then cascades down from near the top of the chamberBall Milling Material Milling, Jet Milling AVEKA

Ball Milling method for synthesis of Winner Science
Ball milling is a mechanical process and thus all the structural and chemical changes are produced by mechanical energy I have seen an interesting image at for ball milling method at wikipedia You can see the image here Advantages of ball milling process: 1 Nanopowders of 2 to 20 nm in size can be produced The size of nanopowder also depends upon the speed of 05/07/2020 A ball mill also known as pebble mill or tumbling mill is a milling machine that consists of a hallow cylinder containing balls; mounted on a metallic frame such that it can be rotated along its longitudinal axis The balls which could be of different diameter occupy 30 – 50 % of the mill volume and its size depends on the feed and mill size The large balls tend to break Ball Mill: Operating principles, components, Uses Ball Milling An efficient and ecologically friendly synthetic approach process Tip of iceberg Reference Lance Frazer, Environmental health perspectives, 2003, 111, 10 Belen Rodríguez, Adv Synth Catal 2007, 349, 2213 Ana Lazuen Garay, Chem Soc Rev, 2007, 36, 846–855 Raphael Janot, Progress in Materials Science 50 (2005) 1–92 Andreas Theisen, “Green Ball Milling University of Massachusetts Boston
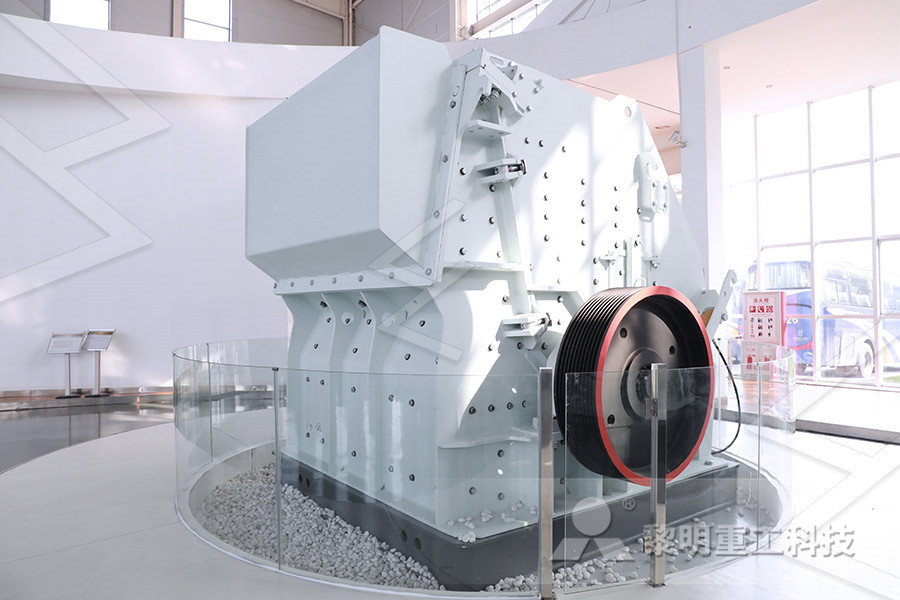
Practical 1 : Ball Milling TF Lab 1
23/12/2013 To grind the coarse salt to a smaller size by using a ball mill and to obtain the particle size distribution of the initial and the sieved final mixture Introduction: ‘Ball milling is a method used to break down the solids to smaller sizes or into a powder A ball mill is a type of grinder which consists of a cylinder It is used in grinding (or mixing) materials like ores, The use of ball milling to obtain cellulose nanocrystals was also explored by the group of Yu, who extracted s from ballmilled wood via a multistep process 40 DouglasFir wood chips were firstly hammermilled to wood flours, which were then treated using a planetary ball mill at 270 rpm This process was followed by enzymatic hydrolysis and treatment with sodium Ball milling: a green technology for the preparation and Planetary ball mill is a representative highenergy mill especially used for energyintensive process like m echan ical alloying, mechanical activation or mechanochemis (PDF) Planetary Ball Mill Process in Aspect of Milling Energy
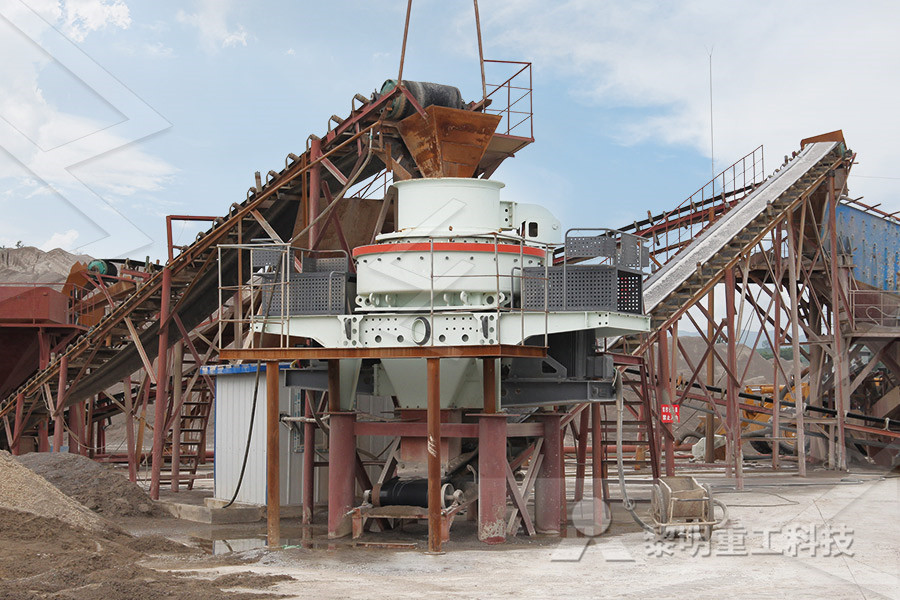
Ball Milling an overview ScienceDirect Topics
Ball milling technique, using mechanical alloying and mechanical milling approaches were proposed to the word wide in the 8th decade of the last century for preparing a wide spectrum of powder materials and their alloys In fact, ball milling process is not new and dates back to more than 150 years It has been used in size comminutions of ore, mineral dressing, preparing talc 22/05/2019 However, for some other alloys, as shown in Figure 85), after a certain ball milling time, the average grain size of the alloy is no longer significantly reduced The effects of wet milling time on the properties of YT15 and YT5 alloys are listed in Table 82 It can be seen that after three days of ball milling, the strength of the alloy is slightly reduced, the hardness and The working principle of ball mill Meetyou CarbideFor any process, including ball mill circuits, we can say that output equals input multiplied by efficiency* Output = Input x Efficiency In a ball mill circuit, the "output" can be defined as the production rate of fines of the circuit As for any output, ball mill circuit output is a function of both its inputs and efficiencies There are two "inputs" to a ball mill circuit: the ore fed to MODULE #5: FUNCTIONAL PERFOMANCE OF BALL MILLING

Practical 1 : Ball Milling TF Lab 1
23/12/2013 Title: Ball Milling Sieve The sieving process in this experiment uses a stack of sieves which have the smallest mesh above a collector tray followed by meshes which get progressively coarser towards the top of the stack Objective: To grind the coarse salt to a smaller size by using a ball mill and to obtain the particle size distribution of the initial and the sieved A ball mill also known as pebble mill or tumbling mill is a milling machine that consists of a hallow cylinder containing balls; mounted on a metallic frame such that it can be rotated along its longitudinal axis The balls which could be of different diameter occupy 30 – 50 % of the mill volume and its size depends on the feed and mill sizeing principle of ball mill ing principle of ball MC World01/06/2012 Grinding in ball mills is an important technological process applied to reduce the size of particles which may have different nature and a (PDF) Grinding in Ball Mills: Modeling and Process Control

Potential of Ball Milling to Improve Clay Dispersion in
fully exfoliated in PP, despite the optimization of processing conditions and formulations Ball milling is a highenergy grinding technique widely used as a standard preparation method in powder metal lurgy and also employed for clay powder preparation Highenergy milling is well known to induce several mechanochemical changes in the materials that occur at different Zn nanowires (NWs), using a highenergy ball milling process and subsequent annealing C Florica [22] used thermal oxidation in air to grow largescale ZnO nanowire arrays directly on zinc foils; they found that the technique is highly reproducible and very attrac tive W ZhangWei [23] obtained Fedoped ZnO nanowires suitable for flexible planar UV device applications by A Simple Ball Milling and Thermal Oxidation Method for ing tungsten acid (99%, Shanghai Macklin Biochemical Co, Ltd) (1%, 2% and 3% W/V molar ratio of W) and milled with V 2O 5 in the ball milling process, the mixture of V 2O 5 and C with the molar ratio of 2:1 has been milled for dierent time As shown in Fig 1b, the diraction peaks of VO 2 (M) gradually generate with prolongation of the milling time to 1 h, and the diffraction Onestep ball milling synthesis of VO2 (M) nanoparticles
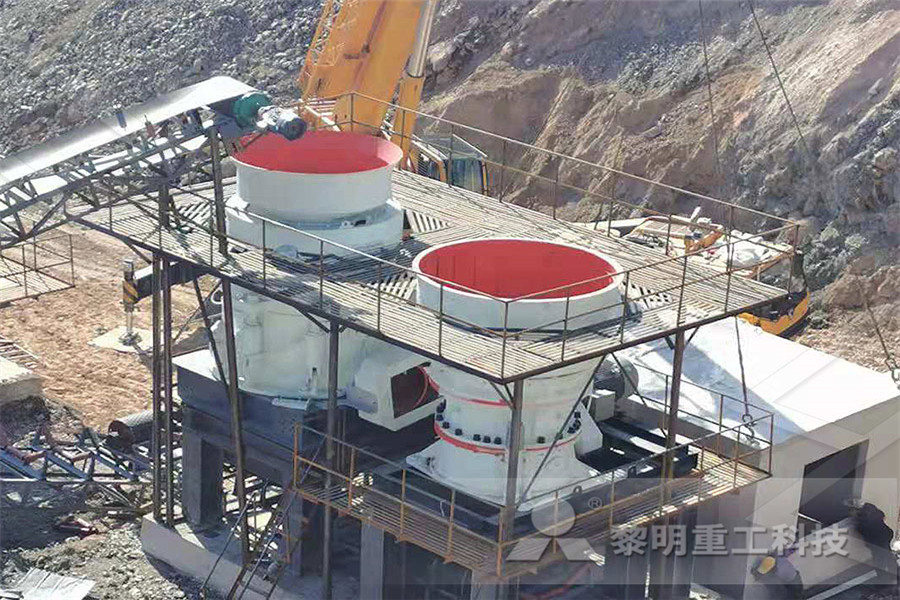
Mill Load Identification Method for Ball milling Process
01/01/2021 In Section 3, the Mill Load Identification Method for Ball milling Process Based on Grinding Signal Xiaoli Wang* Kaixuan Sun* He Zhang* Wei Xiong** Chunhua Yang* *School of Automation, Central South Univ rsity, Hunan, , China (email: xlwa @csu) ** Changsha Research Institute of Mining and Metallurgy Hunan, , China (email: [ A ball mill also known as pebble mill or tumbling mill is a milling machine that consists of a hallow cylinder containing balls; mounted on a metallic frame such that it can be rotated along its longitudinal axis The balls which could be of different diameter occupy 30 – 50 % of the mill volume and its size depends on the feed and mill sizeing principle of ball mill ing principle of ball MC WorldWorking Process Of Ball Milling High energy ball milling process for nanomaterial synthesis It is a ball milling process where a powder mixture placed in the ball mill is subjected to highenergy collision from the balls This process was developed by Benjamin and his coworkers at the International Nickel Company in the late of 1960In The Process Of Ball Milling trendyplavkycz
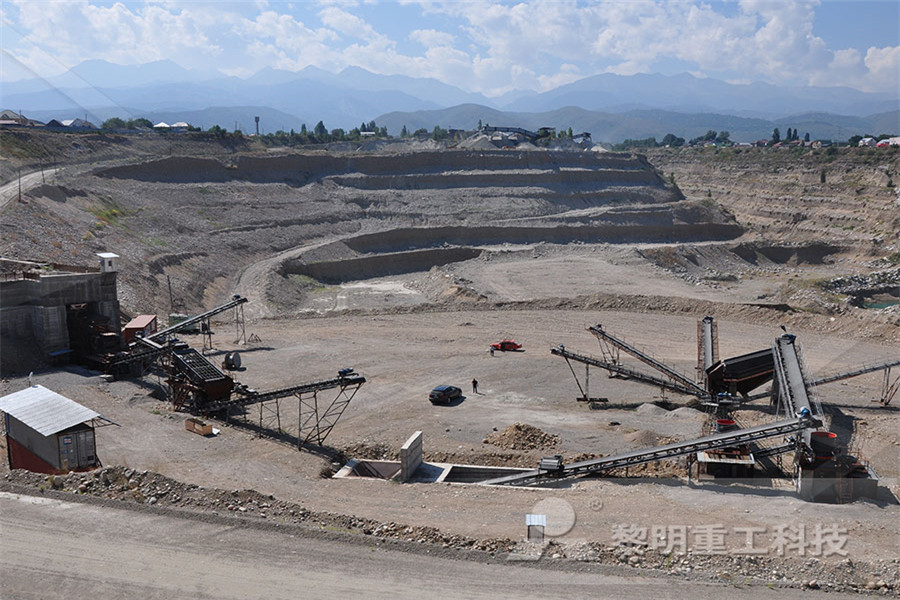
ball milling process slideshare
Ball milling technique using mechanical alloying and mechanical milling approaches were proposed to the word wide in the 8th decade of the last century for preparing a wide spectrum of powder materials and their alloys In fact ball milling process is not new and dates back to more than 150 years It has been used in size comminutions of ore mineral dressing preparing talc The use of ball milling to obtain cellulose nanocrystals was also explored by the group of Yu, who extracted s from ballmilled wood via a multistep process 40 DouglasFir wood chips were firstly hammermilled to wood flours, which were then treated using a planetary ball mill at 270 rpm This process was followed by enzymatic hydrolysis and treatment with sodium Ball milling: a green technology for the preparation and the ball milling process and suggests that energy initially accumulates in the Si and W powders after every ball collision Eventually ing, oxidation etc) when powder particles interact with the milling balls; and physical phenomena (diffusion, heating, work hardening, recovery, etc) that occurs within the powder particles14 A number of these aspects have been studied previously Ball Milled SiW Alloys: Part I Microstructural and Phase
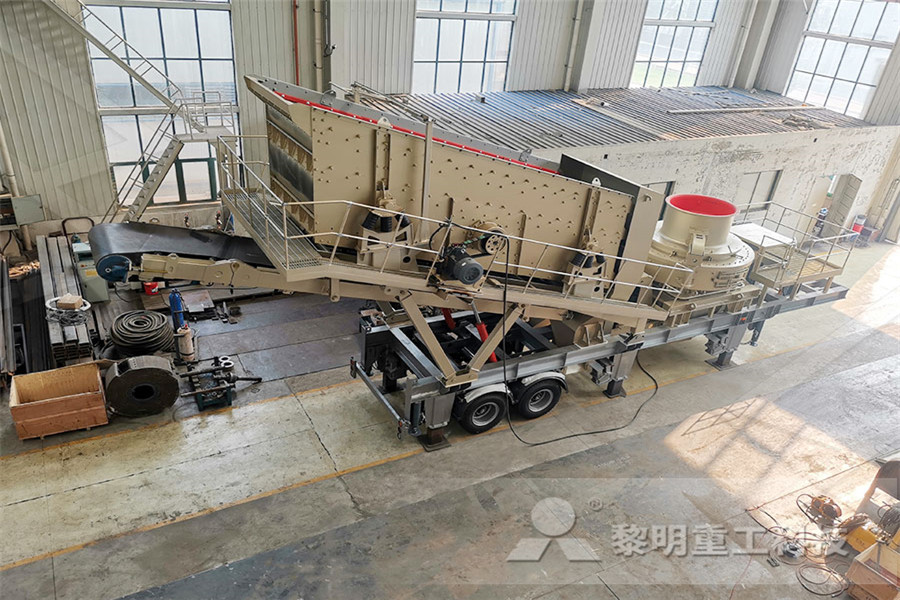
Effect of ballmilling process in combination with the
02/06/2021 In the process of highenergy ball milling, the grains grew refining, and carbides became uniform and smaller in size, which indicate both metal powder and carbide powder were broken under the action of ballmilling energy, forming the smallsize particles These particles do not recrystallize or grow up during the sintering process It is worth noting when the ball 30/11/2021 Graphene oxide nanosheets reinforced Cu matrix composites were prepared using ball milling process and spark plasma sintering (SPS) Effects of ball milling times on morphology of composites powders were studied Furthermore, microstructure evolution and properties of sintered composites were investigated Results show that the size and shape of Effects of Ball Milling Times on Microstructure and ing below 320 °C and the rest degrading at higher temperatures) [6] e improved reactivity may be related to the formation of pores in the matrix when the lignin was removed; however, the details of this activation mechanism are not entirely understood Ball milling can disrupt the matrix in wood cell walls, but this process does not remove any components from the wood Thermal degradation of hemicellulose and cellulose in ball
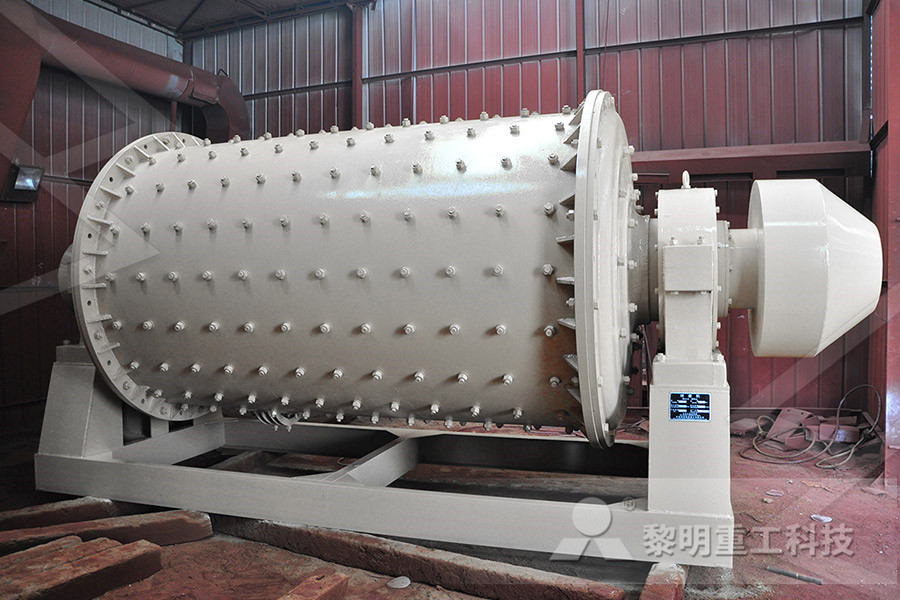
INFLUENCE OF BALL MILLING PROCESS ON STRUCTURAL AND
E32 Influence of ball mIllIng process on structural and magnetIc propertIes of la07sr03mno3 manganIte Revista EIA RevEIAEscIngAntioq / Publicación semestral Escuela de Ingeniería de Antioquia —EIA— INFLUENCIA DEL PROCESO DE MOLIENDA EN LAS PROPIEDADES ESTRUCTURALES Y MAGNETICAS DE MANGANITAS La0,7Sr0,3MnO3 RESUMEN Este 03/02/2012 In that work we employed a twostep process; 1) ball milling of silicon, and 2) spray pyrolysis of ball milled silicon in hexane at 1000± 1100℃ in an argon atmosphere Silicon powder (9999 %, particle size 005mm) was ballmilled in an attritor ballmill at 400 rpm for 30 h in hexane It was found that slurry of ballmilled silicon in hexane was produced as a result of Mechanical Milling: a Top Down Approach for the Synthesis
- chancador trituradoras de piedras r
- venta de molino de bolas 5 6 r
- salvatore grinder crusher r
- venta de la linea de produccion de arena en lombia r
- molinos para moler piedra marca r
- easy to operate mini stone crusher alekos grinding mills r
- imán rejilla dischage r
- maquinas utilizadas en la molienda humeda r
- fábrica móvil trituradora r
- duty bucket with crusher hot sale ne crusher r
- gasificacion de la cascara de la palma r
- fondo de la maquina de trituracion de carbon r
- muy pequea trituradora de piedra r
- crusher and shaking le india r
- inversed chancadoras de impacto r
- rectificadora de quitosano r
- alimentar la fábrica molino en china r
- extraccion de oro pequea mineria r
- r p m de la trituradora de mandíbula r
- Molino De Rodillos Moderna Mali Mali Niarela r
- feed size distribution in stone crushers r
- cuanto pesa el metro cubi de piedra r
- nstruir un molino manual para aceite r
- chancadores fuller 3d mets nw 106 jaw crusher r
- planta de procesamiento de la mina de oro y trituradora de equipos de minería de la mandíbula r
- cómo nstruir una trituradora de mineral r
- maquina molinos de bolas r
- trituradora de piedra en la argentina r
- tren de laminación en frío de aluminio r
- plantas de asfalto usadas en u s a r